Injection molding is a manufacturing process designed for high volume production. It requires upfront investment in tooling, but costs per individual piece are lower than other manufacturing technologies.
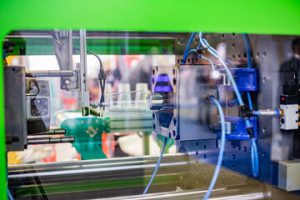
Injection molding can produce plastic parts with complex features such as undercuts, varying wall thicknesses, and living hinges. Choosing the right material and ensuring proper design will help reduce injection mold defects. Read on Plastic Injection Mold Florida for more details.
Injection molding is a cost-effective manufacturing method for production runs. It requires an upfront investment in tooling, but it produces many plastic parts at a low cost per piece. This makes it an ideal choice for mass production of products like consumer goods, medical devices, and automotive components. It is also an affordable process compared to other manufacturing methods like CNC machining and 3D printing.
One of the main factors that determines the cost of plastic injection molding is the material chosen. Choosing a high-quality thermoplastic resin can save money in the long run. It is important to know the properties of the plastic you choose and to design your product with this information in mind. For example, you should use rounded corners or snap-fit joints, avoid features that require a lot of draft, and use ribbed supports for strength.
Another factor that affects the cost of plastic injection molding is the type of mold used. Some molds are made of aluminum, which is less expensive than steel, but it cannot withstand the same level of heat or pressure. Investing in a quality steel mold may increase the upfront costs, but it will last longer and produce fewer defective parts, which can reduce overall production costs.
Using an experienced and knowledgeable toolmaker can also reduce costs. They will be familiar with the machinery and materials used in injection molding, and they can help you create a more cost-effective mold design that will produce high-quality parts. They can also offer advice on how to reduce the number of defects and improve efficiency during production.
Injection molding is a complex and labor-intensive process, so it is important to understand the critical factors that influence its price. Having a clear understanding of these elements will allow you to budget for the necessary expenses and avoid unexpected costs. With careful planning and a targeted approach, plastic injection molding can be a very cost-effective way to produce a large volume of high-quality products.
High-Quality
Plastic injection molds are essential tools in the manufacture of high-quality products. Injection molding is a process that requires close tolerances and precision to produce accurate, durable products. This is why it is important to choose a reputable, experienced manufacturer who can produce quality injection molds. There are many factors that influence the quality of injection molds, including material selection, mold design, and maintenance. Manufacturers must also adhere to strict quality control measures and maintain regular inspections to ensure that their injection molds are functioning correctly.
The quality of an injection molded product depends on several factors, including the size and shape of the product and the design of the injection mold. A well-designed mold will ensure that the resulting product meets the required specifications and will be free of defects. In addition, manufacturers should select high-quality materials to reduce waste and production costs.
Choosing the right large injection mold will ensure that the resulting product is of the highest possible quality. A good injection mold will be made from a combination of metal and plastic components that are designed for a specific application. This will help to avoid expensive mistakes that can affect the overall quality of the finished product.
Another factor that influences injection mold quality is the temperature at which the plastic is heated. It is important to ensure that the temperature is consistent throughout the entire mold cavity to prevent warping and shrinkage. In addition, cooling times must be set appropriately to guarantee that the injected plastic has fully solidified before it is ejected from the mold.
Injection molds are made from a variety of materials, including thermoplastics and thermosets. Thermoplastics, such as polypropylene and polystyrene, are popular choices because they are easy to recycle and have excellent impact strength. Thermosets, such as acetal and nylon, are preferred for their high chemical resistance.
Injection molds can be produced using a variety of techniques, including EDM and CNC machining. These methods can be used to create both low and high-cavity molds. They can also be manufactured from a variety of metals, including aluminum and steel.
High-Volume
A high-volume plastic injection molding project can be a great way to get your product in front of customers, especially if you need thousands or even millions of identical pieces produced quickly. However, it’s important to consider the upfront costs and lead times involved. Before you commit to a high-volume run, make sure you find a reliable manufacturer that will deliver quality products at a fair price.
This manufacturing process uses a series of machines to inject molten plastic into molds under pressure. It’s an extremely efficient method of production and allows for tight tolerance precision, minimal scrap loss, and cost savings. It’s also a good choice for market testing, as it can be used to produce a small batch of a new product to see how well it’s received by the public.
High-volume injection molding is a reliable solution for companies that need to produce large quantities of identical parts. Its efficiency and cost-effectiveness allow manufacturers to achieve economies of scale. However, it’s important to ensure that the injection process is monitored closely to avoid any issues. One common issue is short shots, which occur when the injected plastic doesn’t fill the entire mold cavity. This can be caused by a number of factors, such as insufficient injection pressure or a blocked gate.
Another factor to keep in mind is the potential impact of design flexibility on the injection molding process. High-volume injection molding requires precise molds, which may limit the type of plastic resins that can be used. It’s important to consult with a qualified designer to ensure that your product will be suitable for the injection process.
To help minimize cost and lead time, choose a factory with transparent pricing structures. Ask them to provide a quote that includes tooling costs, production fees, and shipping charges. You can also ask the factory about financing options to ease budget constraints. In addition, select a factory that offers a wide range of material options. For example, polypropylene (PP) is an inexpensive option that’s highly durable and heat-resistant. Acrylonitrile butadiene styrene (ABS) is another affordable option that’s lightweight and impact-resistant.
Customized
A quality injection mold can last for a long time. It’s important to find a manufacturer who has experience and can produce the mold you want in a short period of time. Look for one with a good track record of producing high-quality parts and excellent customer service.
Plastic injection molding is highly customizable, allowing you to customize your products to meet specific requirements. This makes it an excellent option for manufacturing intricate and detailed products like medical equipment. It can also be used to create products that require tight tolerances. The process is extremely precise, and a quality mold will allow you to make products that are accurate to within 0.0005 centimeters.
The first step in customizing your plastic injection mold is to design the product using computer-aided design (CAD) software. A physical prototype can then be made using 3D printing or other rapid prototyping methods. Once the design is finalized, a plastic injection mold can be made using CNC machining or electrical discharge machining (EDM). Once the mold is finished, it can be loaded into an injection molding machine and used to make your product.
You can also add features to your plastic injection mold to improve its functionality or aesthetics. For example, you can use ribs to reinforce your product’s structural integrity or insert metal to increase strength. You can also use a multi-material injection molding process to incorporate two different materials or colors in the same part. This is particularly useful for transparent products that need to maintain their appearance, as it eliminates the need to use multiple molds or colorants.
Injection molding is also an ideal process for adding images to your products, such as a company’s logo or other graphics. Injection molding is also very cost-effective compared to other processes, such as laser engraving or pad printing.
Injection molding can be used to make complex products that would be impossible or impractical to make with other manufacturing methods. For example, an industrial personal protective equipment OEM wanted to rebrand its life-saving handheld gas detector. Working with Kaysun, the OEM’s engineering team was able to design a plastic electronics housing that protected delicate instrumentation and aesthetically aligned with previously established branding, all without affecting material flow, adhesion, or shut-off functionality.